Contents
What is Industrial refrigeration system?
Industrial refrigeration systems are heavily used in supermarkets, airports and provision stores for storing a wide variety of foods, vegetables, and frozen products using multiple evaporators set at different temperatures.These systems can remove a large amount of heat, thereby lowering the temperature of a large refrigerated space to approximately -25 degrees Celsius.
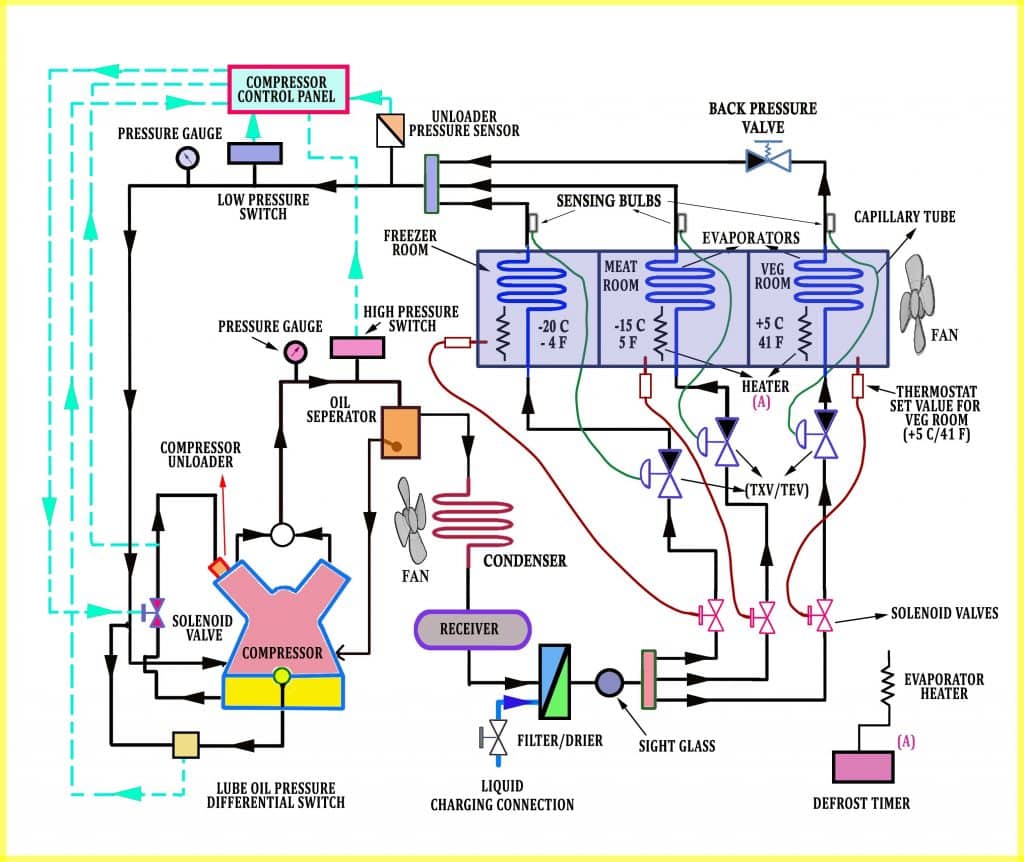
Industrial Compressors
Large refrigeration compressors usually consist of 2 to 4 cylinder units to handle large refrigeration plants.
Only some compressor cylinder units are provided with unloaders so that refrigeration capacity can get adjusted as the food stock starts becoming cold.
The commercial refrigeration system consists of thermostats, solenoid valve, a thermostatic expansion valve (TXV or TEV) or metering valve and back pressure valve with safety devices such as LP cut out, Â HP cut out, Lube oil cut out and compressor unit unloader.
Large industrial refrigeration plants have a commercial freezer and Meat room with the temperature maintained at -20°C or -24.8°F  and -15°C or 5°F, hence temperature is sensed by thermostats.
Where’s Vegetable room thermostat set at +5°C or 41°F.
A thermostat has two functions one is to immediately stop the cooling of refrigerated room, and another one is to start the cooling operation of less cooled refrigerated room.
All is done by operating the solenoid valve to close and open the flow of refrigerant to the refrigerated room.
Solenoid valves are controlled by the thermostats attached at each refrigerated rooms.
- Commercial Freezer room
- Meat room
- Vegetable room
How does an industrial refrigeration system work?
Generally, for commercial freezer room and meat room or any refrigerated space, the thermostat differential temperature setting is set at around 5°C.
Which means, the solenoid valve opens and starts to increase cooling for the freezer room when its temperature drops to -15°C (ie 5°C drop in temperature).
The same goes for the meat room at -10°C.
Similarly, the solenoid valve opens for the vegetable room at (7°C).
The thermostatic expansion valve(TEV or TXV) adjusts the degree of superheat; so that evaporator may not starve of refrigerant.
Why is it important to use a backpressure valve?
A back pressure valve is fitted at the evaporator outlet for the vegetable room since vegetables are sensitive to excessive changes in temperature, which could damage these perishable food items.
Therefore, a positive temperature is maintained in the vegetable room to keep the vegetables fresh and undamaged.
The back pressure regulator valve keeps the rate of evaporation reduced to provide a gradual cooling.
It also creates back pressure on the evaporator coil, to ensures that most of the liquid refrigerant is made available at lower temperature zones ie. freezer and meat room.
Back pressure valves are spring loaded and a non-return valve.
Case 1: Stopping of the refrigeration system
Now, let’s consider the meat room achieves its temperature of -15°C then the solenoid valve to this room closes which leads to a drop in suction pressure at the compressor.
Drop in suction pressure activates the unloader to unloads one of the compressor units and keeps the unit cut off by lifting its suction valve open.
Thereby reducing the compressor capacity and not allowing the compressor motor to stop on a low-pressure trip.
Hence maintaining vegetable room cooling continued with one of the compressor units under unloaded condition.
When the vegetable room thermostat comes to its set temperature of + 5°C, the solenoid valve for the vegetable room evaporator closes which leads to dropping in the suction pressure.
Considering the other two solenoid valves of meat and freezer room closed by the thermostat, it triggers the low suction pressure cut out switch to stop the refrigeration compressor.
Case 2: Starting of the refrigeration system
Let’s say temperature starts rising for the freezer room or meat room or veg room then, the solenoid valve for that room will open, increasing the suction pressure which triggers the low suction pressure cut out switch to reset and start refrigeration plant for cooling.
Case 3. Safety devices in an industrial refrigeration system
Now, for some reason discharge pressure increases due to liquid refrigerant entering in refrigeration compressor, then the system is protected by a High pressure switch.
Thermostatic expansion valve or metering valve always ensures vapour refrigerant enters in the compressor suction as a liquid refrigerant when compressed can damage the compressor.
Oil pressure sensor:
Also, the compressor is protected against the drop in Lube oil pressure too, by oil differential pressure sensor.
Oil pressure sensor senses refrigerant suction pressure and crankcase lube oil pressure.
The lube oil pressure must always be greater than the suction pressure, because if the suction pressure becomes higher than the lube oil pressure, then the suction pressure starts to restrict the lube oil pressure to flow between moving parts of crankshaft leading to mechanical damage of bearings.
Therefore, the lube oil pressure is set at 2 bar above the suction pressure of the compressor.
Electric heater for defrosting
Around the evaporator coil, electric heater for the defrosting is also fitted, these are timer operated at least twice a day, so that ice formed on the evaporator coil is defrosted and drained.
Also, pan heaters collect the melted ice from the evaporator drain tray.
Routine maintenance in an industrial refrigeration system:
- Check for defrosting.
- Oil level check.
- Low Pressure switch test check.
- High Pressure switch test check.
- Differential Lube oil pressure test check.
- Gas leakage check.
- Oil leakage check.
- check drive belt tension
- Compressor vibration check.
- Filter /drier cleaning, replace Silica Gel/desiccant if required.
- Solenoid valve and expansion valve filter to be cleaned.
- Trips to be tried out.
- Oil filter to clean in the crankcase.
- Gas charged or oil charge as required.
- Condenser cleaning once in 6 months.
I have learnt a lot on this site and this is the best site.I like this site a lot.